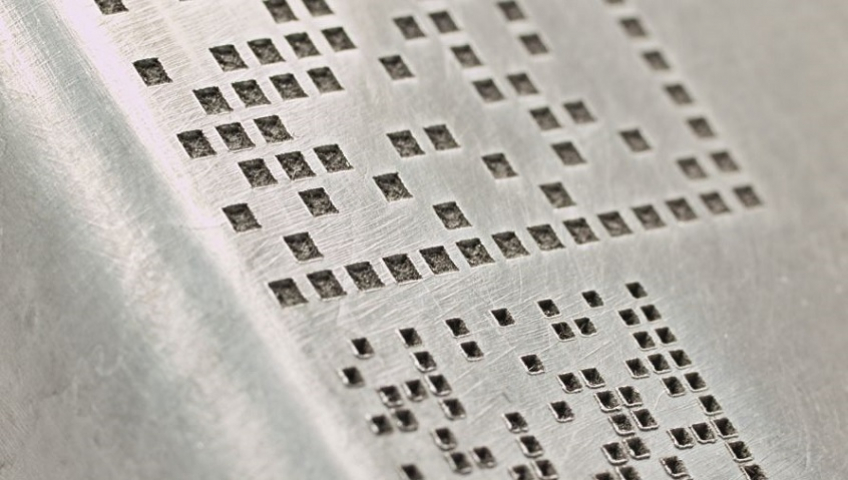
Laser a traceability
Bezchybná výroba je cílem každé výrobní společnosti. Bohužel trvalá existence možnosti selhání zařízení či obsluhy naznačuje, že vytvořit výrobu naprosto bez chyby jednoduše nelze. Lze však vliv chyby na výrobu co nejvíce eliminovat. Z těchto důvodů se zavádí pojem traceability, tedy sledování průběhu výroby a sběr dat z tohoto sledování. Traceability umožňuje včas rozpoznat chybu ve výrobě a určit původ a důvod jejího vzniku. Díky tomu lze předejít vzniku dalších defektních kusů a současně vyřadit již vyrobené díly, které snižují kvalitu dodávky. Dosah traceability však může být ještě významnější – umožňuje např. i zpětné dohledávání v případě vzniku zákaznické reklamace. V takovém případě je možné ze shromážděných dat určit, co mohlo být v minulosti příčinou vzniku reklamované chyby a výrobce tak může včas stáhnout zpět ke kontrole všechny díly, které s reklamovaným dílem sdílely výrobní proces v nejbližším časovém horizontu.
Traceability je zpravidla součástí MES systému ( Manufacturing information systems ) pro automatizaci výroby. V rámci sledování výrobků nese každý z dílů svoji vlastní identifikaci, podle které je rozeznáván. Jak díl prochází jednotlivými výrobními procesy, je aktualizován jeho výrobní status. Informační systém si tak vede záznam dílu pod jeho identifikační značkou o tom, jakými procesy již díl prošel a jak úspěšně.
Aby bylo možné správně zavést traceability, je nutné nejprve zajistit klíčový prvek - samotnou identifikaci dílu. Identifikace může mít mnoho různých podob a mohou na ní být kladeny rozličné požadavky. V případě automatizovaných výrob se nejčastěji využívají k identifikaci čárové kódy – ty mohu nést variabilní kódovanou informaci a mohou být jednoduše strojově čteny. V dnešní době jsou zdaleka nejpoužívanější 2D čárové kódy typu Datamatrix, umožňující nést velké množství informací na malé ploše a obsahují algoritmus pro opravu vlastních chyb, díky čemuž mohou být načítány i při jistém stupni poškození.
Pro vytváření identifikačních značek se nejčastěji využívá laserového značení z mnoha důvodů. Prvním z nich je obrovská variabilita – vzory lze velmi jednoduše měnit a editovat, což je při značení pomocí čárových kódů potřeba, protože kód na každém dílu nese jiné informace a má tedy i jinou podobu. Zpravidla je obsah kódovaných informací posílán laseru z databáze výrobce jen těsně před tím, než se provede popis. Druhým důvodem je fakt, že laser vytváří velmi odolné až nesmazatelné popisy, protože svým působením ovlivňuje a mění materiál přímo. Zatímco v některých případech je požadavek na čitelnost identifikace dílu po celou dobu výrobního procesu, jindy musí být čitelnost zaručena po celou životnost dílu, aby byl díl rozpoznatelný i při jeho případné reklamaci. Mezi obrovské výhody pro provoz laseru patří v neposlední řadě i jeho bezúdržbovost a absence jakéhokoli spotřebního materiálu.
Existují provozy, kde je vytváření dílů složitější vzhledem k určitým požadavkům na jakost dílu. V některých případech je potřeba např. zachovat koroziodolnost materiálu i po tepelném ovlivnění laserovým paprskem, jindy je zapotřebí vytvořit kontrast pouze v několikamikrometrové ochranné vrstvě dílu bez jejího výrazného narušení nebo provést komplikované značení jen ve velmi úzkém času napnutého výrobního taktu. V případě, že má být díl po označení vystaven povrchové úpravě, je vytvořit popis do materiálu naopak co nejhlouběji, aby byl čitelný i po ní - pro tuto operaci se používá metoda tzv. laserového gravírování, kdy je popis jistých parametrů cyklicky opakován tak dlouho, dokud není sublimován materiál až do požadované hloubky.
Právě jednu z aplikací laserového gravírování je možné předvést jako konkrétní příklad. V okamžiku, kdy jeden z výrobců hliníkových dílů hledal možnosti jejich identifikace pomocí 2D kódu pro zabezpečení traceability, byl navržen a optimalizován laserový proces jako náhrada mikroúderového značení, které nedosahovalo požadovaných kvalit kódu během jeho čtení. Protože je hliníkový odlitek po označení otryskáván, bylo zapotřebí zavést kód do dostatečné hloubky, aby byla i po otryskání zachována jeho čitelnost. Pulsním vláknovým laserem tak byl vytvořen Datamatrix kód o velikosti 18x18mm do hloubky 0,15mm a v taktu 30s udaným zákazníkem, po otryskání bylo pak úspěšně ověřeno jeho čtení. V závislosti na rozměru DMX kódu je možné docílit hloubky až 0,5 mm.