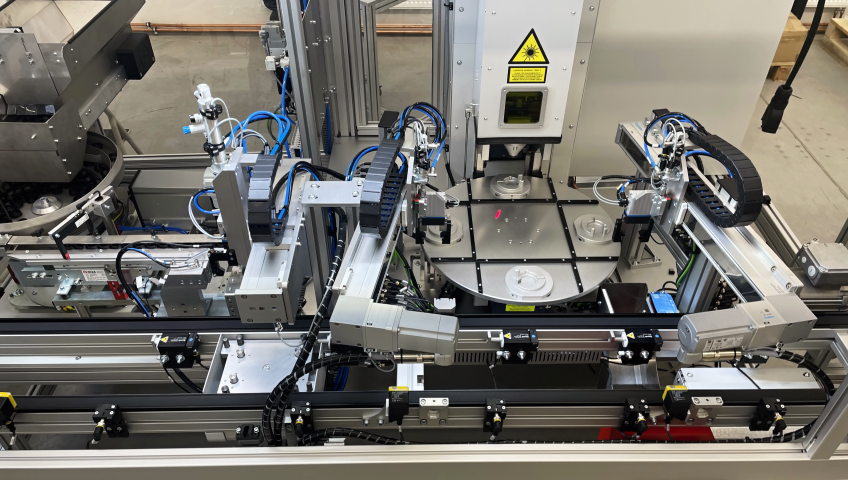
VIDEO: Automated stations for assembly and laser welding of plastics
In today's competitive environment, efficiency, productivity and quality are paramount. Automation can significantly increase productivity levels by streamlining and speeding up production processes. For this reason, many of our customers are also automating their production. This time, we designed and built two fully automated stations for processing booster valves used in truck cooling systems. The stations designed by LINTECH became the third and seventh in the customer's production line.
Design of the automated stations:
To meet the customer's specific requirements, two fully automated segments were designed and integrated into the existing production line. The stations are bilaterally connected to a closed conveyor system, which ensures a smooth material flow. This design choice enables efficient processing while minimizing downtime and maximizing throughput.
First station: assembling and welding the plastic ring
The first station assembled, the third station of the production line, focuses on assembling and welding the plastic ring to the valve body. Four types of parts are welded in the station, each requiring a different orientation of the ring to be welded. A complex system was designed to address this challenge. This system uses a vibratory tray where the ring is precisely oriented using an overflow groove and a subsequent mechanism where the ring is rotated to the desired angle relative to the initial orientation from the vibratory tray using grippers located on the rotary axis. An uninterrupted workflow is ensured by automatic refilling of the rings into the vibratory pot from a bunker with sufficient capacity.
Once the ring has been properly clamped with a force of 250 N, the part and ring are advanced into position to undergo laser welding. Under a constant pressure of 700 N, the entire part is spun up to a speed of 12 revolutions per second and our 300 W welding laser is triggered. After cooling, the part is moved back onto the conveyor pallet using a manipulator. By using a carousel system, the operations of setting up, welding and unloading the part back onto the conveyor pallet are carried out simultaneously, reducing the cycle time to 12 seconds and thus increasing the overall productivity of the machine.
Second station: assembly and welding of the valve spool
The second station assembled, the seventh station of the production line, is responsible for assembling the spool to the booster valve. Upon arrival, the part is thoroughly inspected to verify its completeness and proper foundation. The coils are oriented in several positions on the conveyor pallets. Once the coil is correctly rotated, it is pre-pressed onto the valve with a force of 200 N. The complete assembly is moved by manipulator to the carousel where the coil is rotationally welded to the valve under a pressure of 2000 N. The welding process is carefully monitored, with special attention paid to the final crimping depth after welding. Precise measurements are compared with established values to ensure that quality standards are met. If any deviations are detected, the part is automatically removed from the production line by a manipulator and redirected to the NOC box. This strict quality control ensures that only components that meet the highest standards continue in the production process.
LINTECH, takes great pride in successfully meeting the demanding requirements of its customers and partners. This successful partnership underlines the importance of tailor-made technical solutions in achieving production efficiency in today's competitive market.