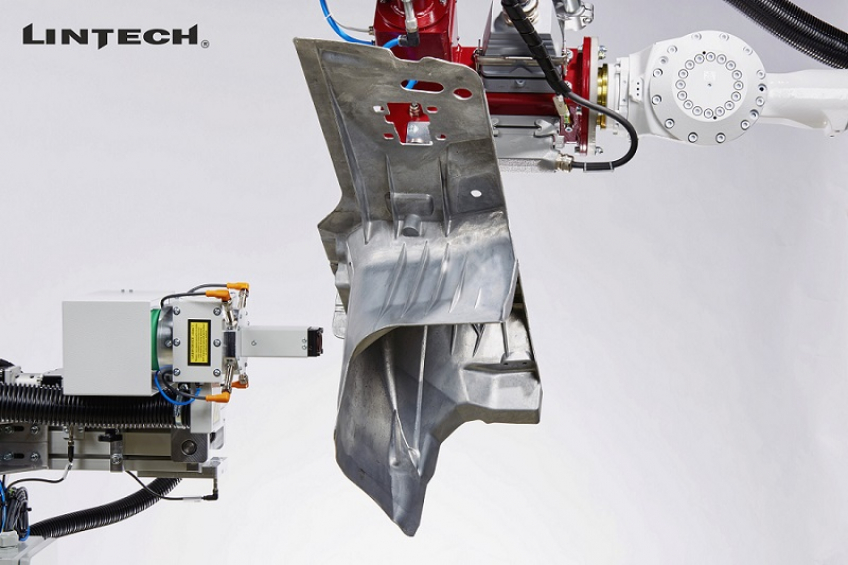
Case study: SPI module integrated into laser safety head designed by LINTECH
LINTECH has worked closely with SPI Lasers for many years. As a laser module integrator, LINTECH uses the SPI laser system mainly for marking and engraving applications. In addition to the production of laser systems, LINTECH also offer their customers the services of a design centre. As one of the few companies on the Czech market, they can offer a comprehensive solution to the challenges of laser manufacturing production. From consultancy, through solution design, to the final delivery of a complete laser device. Unlike their competitors, LINTECH can design solutions individually, according to the specific demand and requirements of the customer.
LINTECH’s main area of expertise is in the automotive industry, which is widespread in the Czech and Slovak Republic. Over the last few years, they have been working together with their German partner to expand their field of activity, as a consequence they currently deliver laser systems throughout Europe. One of the main reasons for this success is their technical background and the expertise of their inhouse application laboratory, that enables them to keep up with SPI’s fiber laser innovations.
New task for LINTECH engineers
A few years ago, at one of the trade fairs which LINTECH regularly participates, they spoke with a new customer who asked them to propose a laser based solution to update his marking production process. The existing process centred around creating a mechanical mark on an aluminium casting. The process was complicated by the fact that the micro-dot marking technology currently being utilised was located at a separate work station to the casting process and the movement of the part to the microdot marking process was a purely manual process; this would often lead to misalignment and therefore errors in the positioning of the microdot. LINTECH’s task was to create a robotic process offering an improved marking process whilst simultaneously eliminating the risk of error brought about by the manual manipulation of the part.
The solution proposed by LINTECH was to design a robotic laser device that engraved the datamatrix code into an aluminium casting immediately after being removed from the casting machine, at the very beginning of the manufacturing process; removing the need for the manual movement and positioning of parts. Marking at this point in the production enables all the required information to be promptly 2D marked without error.
From a technical perspective, the solution has brought several challenges. The product is removed from the casting machine by a robotic arm and is subsequently cooled in a water bath. However, even after cooling, the product temperature is over 100°C. Additionally any residual water on the surface must be removed to ensure process stability. In some cases this water bath is removed from the process, meaning the product can go from the casting machine straight to the marking stage, where the temperature of the workpiece exceeds 200°C. Due to these variations in process and the extreme temperatures of the workpiece the safety aspect of the manufacturing process had to be addressed – the proposed equipment had to meet safety class 1.
Why choose laser instead of microdot?
In most cases, the marking of such castings is done by using microdot technology. The microdot creates small dimples in the castings using a hard carbide tip, each representing a single module in 2D code. The material is pushed relatively deep under the surface of the part by the tip, which ensures high resistance of the marked code. The geometry of the hole depends on the shape of the point, especially its angle of grinding.
In order to achieve stable readability of the 2D barcode, it is necessary to create sufficient contrast between the affected and the unaffected material. It is not possible to create a contrast by changing the colour of the surface, as the surface of the workpiece is eventually heavily treated which would result in the colour disappearing from the surface. The microdot does not colour the surface of the material but creates a shadow inside the punched pits by illuminating them appropriately to simulate a dark effect on the surface.
A similar principle for creating 2D code was used with a pulsed laser. A sufficiently powerful pulsed laser can engrave modules in aluminium material with similar efficiency as a microdot. However, unlike a microdot, laser-engraved modules have several advantages.
The laser is very accurate and has a high repeatability as it offers a non-contact process with no associated tool wear. This makes all the modules the same, which makes reading easier. The laser-engraved module´s walls have much greater perpendicularity, so the shadows are better formed. The depth of the engraving is dependent on the number of repetitions of the process and is therefore well scalable to achieve the most optimal time-to-depth ratio. Lasers can also engrave very complicated accompanying patterns or logos. Unlike a microdot, where the punch tip can break off on contact with the material, resulting in a false mark. By contrast, the laser process is extremely robust and stable; since the laser makes no contact with the work piece during the process. Unlike the microdot, there is also no need to clamp the part during the marking process, therefore improving production time and reducing the risk of any manufacturing defects.
Consequently, the quality of engraved codes by using a pulsed laser reach better values during the verification process than micro-dot codes, especially after subsequent surface treatments. It has been shown that an engraving depth of between 0.2 – 0.3mm is required to ensure readability even after surface treatment, which can be achieved in about 10 seconds by using SPI redENERGY100P-EP-Z laser system, with process times of course highly dependent on code size and segmentation. Due to its beam quality of M2 <1.6 and the high 100W average power, the 100P-EP-Z has proved to be very suitable for the entire operation.
To provide a further improvement in process efficiency and cycle time SPI offers higher average power options such as the 200W EP-Z laser for this application.
Solution
In order to achieve the tight production cycle, it is necessary to use a pulsed laser with at least an average value of 70W for engraving; using higher powers would enable further reductions in the processing time. Based on long-term testing, the 100P-EP-Z was selected as the most suitable laser for this application. Compared to the 70W variant, the efficiency increase was around 30%. The F-theta 210 lens was used as the focusing optic.
This lens not only has a suitable focusing distance due to the design of our enclosure, but also has a good ratio between laser spot size and area energy density. This enables large quantities of material to be engraved per unit of time efficiently and in a controlled manner.
Using a new process presents new challenges, but these can be successfully solved using appropriate procedures and design features. The greatest challenge is to meet the necessary safety standards for working with lasers, where the working environment must be effectively protected from the laser beam to meet safety class I. This is provided by several sensors located on a special laser head cover that shuts off the laser whenever a leak is detected. Since laser engraving generates a large volume of impurities, they must be extracted effectively during the process so as not to block the laser beam directed towards the engraved surface.
Conclusion
The final compact cover head designed by LINTECH has passed all stress and safety tests and has therefore succeeded in tenders at the expense of domestic and foreign competition. The performance of the LINTECH cover head and the SPI pulsed fiber laser solution has resulted in exceptionally positive customer feedback, resulting in LINTECH being able to extend the integration of these compact cover heads into customer’s additional production plants, and as a result their global reach continues to expand.
LINK to the Case study on SPI website.