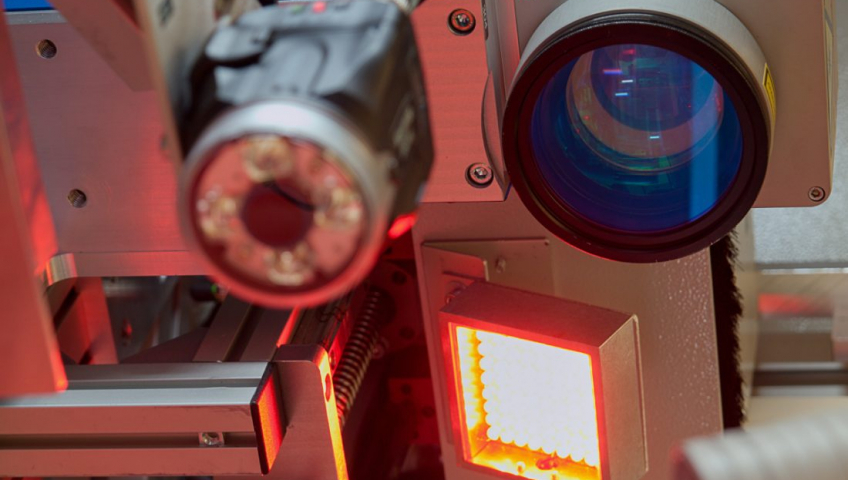
6 questions and answears on the machine vision and the laser technology
The main topic of our article is the machine vision. To collect as much information as possible we have interviewed one of our programmers. Continue reading and maybe you will also find answears to your questions.
1. What is the machine vision?
Simply put, it is the use of a camera for the automated quality control. The machine vision is added to the lasers we construct in order to reduce the labor costs and increase profitability. One of the advantages of these machines is their functionality. In comparison to human workers, the machines are more accurate, faster and they can work non-stop.
2. Why is it generally good to have a laser technology with the machine vision?
The machine vision can be used for:
- VALIDATION (this will prevent further production of pieces that are not suitable for this plus it can prevent the operator error)
- control of a piece for laser marking – its size, specific production parameters – to achieve the requested size etc.
- the selection of the production process (product recognition), followed by the automated device setting
- VERIFICATION (checking of the production correctness)
- most often the verification of the laser marking – quality check, positioning, layout, readability, by the 2D codes determination of the quality requirements of the customer
- CORRECTION (of the manufacturing tolerance and the tolerance of the clamping/positioning of the piece)
- laser marking of a predefined part of the product which may vary based on the specification of the product, way of clamping the piece, its complexity and size (the machine vision helps to check everything that the humans can´t and also in a shorter time)
3. With what applications do you work the most often? (looking for the right position, comparison, reading, verification, control…)
If we integrate the machine vision then we try to reach its maximum potential which means that all the applications are closely related and it´s not possible to pick one. However if I had to mention one thing, then it would be the validation of the correct clamping of the piece before the marking and the verification of the marking itself.
4. Is it possible for the control mechanism to be integrated into the already existing laser system?
It is not always possible. It depends on the construction, data interface and HW equipment. For a successful implementation of the optical system we need a really good HW (a computer to run the SW), a method for communication with the rest of the device and space for the suitable lighting and all the single components of the optical device.
5. Which types of cameras, scanners and checkers do you use and what are they used for?
Based on the laser application, the following products can be integrated into our devices:
- CHECKERS
- validation of the piece before the marking. See above.
- SCANNERS
- control of the 2D code
- selection of the production process – to check if it is the right product
- SMART CAMERAS
- widely used, no further know-how is required
- a controller is needed which requires more space in the distribution board
- they doesn´t offer as many configuration options as we sometimes need
- with more functions being added, the device is more expensive and more difficult to use
- CAMERAS
- a large HW portfolio
- industrial solution
- many SW options
- they can replace all the above
- it is more difficult to work with them
- THERMAL IMAGING CAMERAS
- they have the same features like the smart cameras but they provide thermal data – it´s practically a sensor, rather than a camera
- can be used during the welding process (can be replaced by a different technology)
6. How to archive data and what is the use of LinMARK?
LinMARK can be used as:
- DATA INTERFACE – To enable easy work with difficult data structures linked to the products.
- AUTOMATED SW SAMLIGHT OPERATION – Due to the high demand for genericity of the marked data LinMARK can automate almost all the steps (while the setting of the instruction of the laser) that would normally have to be done by hand. There are different approaches used in different laser applications, however with the use of LinMARK, it is possible to work very sophisticated, fast and there is no need of trained staff. Also it is how we minimaze errors – e.g. creating images of the right size – there is no need to enter the data manually using a keyboard but often they can be generated and calculated automatically.
- COMMUNICATION INTERFACE – Some of our customer´s devices and systems are not compatible with the communication options of our PLC (programmable logic controller). LinMARK (that is developed for the .NET Framework – Windows platform) enables the communication between those systems. In case of the use of the cameras (not the smart ones) it can be used for their operation.
- USER INTERFACE – We try to keep the design, layout and functions very similar to what might already be familiar to the users e.g. from their mobile phones. LinMARK often alternates with the commonly used HMI and it provides the user of the device with tools for its configuration, settings and maintenance.
- TO ARCHIVE DATA – The information about the production itself, evaluation of the pieces, records of the numbers and single production steps of the device. The customers often prefer various formats and ways of archiving data. LinMARK, as a customised application, is very variable and therefore it´s a good solution. Different methods are used for the data archiving such as text files or SQL (Structured Query Language) database in the cloud.
For more information, contact our technical and sales representatives.