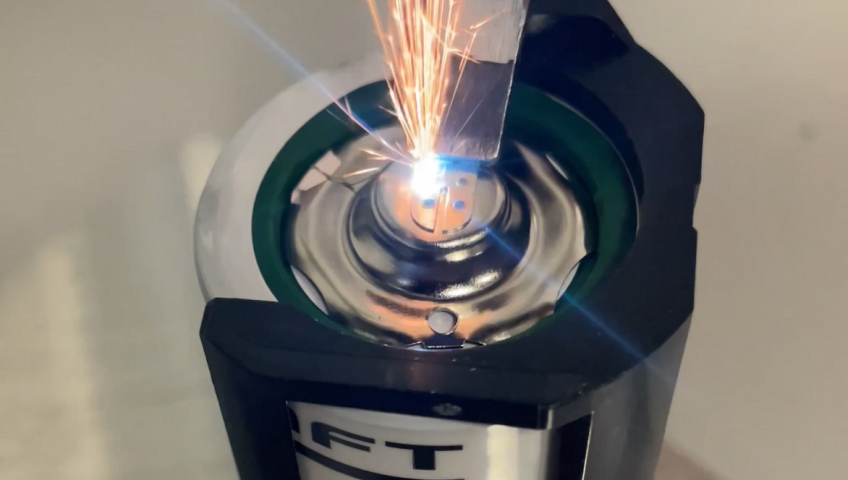
Verbinden von Batteriezellen mittels Laser
Das Laserschweißen von Metallen ist eine der wichtigsten und entsprechend gut untersuchten Laseranwendungen. Bisher basierte diese Anwendung im herkömmlichen Sinne hauptsächlich auf dem Einsatz von kontinuierlichen Hochleistungslasern zusammen mit einem entsprechenden Laserkopf und der dazugehörigen Prozessoptik.
Zum Metallschweißen werden heute jedoch zunehmend gepulste Laser eingesetzt – meist Festkörperlaser, in Kombination mit einem Ablenkkopf und einer F-Theta-Linse. Gerade in den etablierten Anwendungen des Schweißens von Materialien mit großen Dicken, wo es darauf ankommt, einen hohen Wirkungsgrad zu erreichen, werden kontinuierliche Hochleistungslaser natürlich weiterhin ihre Anwendung finden. Es gibt aber auch Anwendungen, wo relativ schwache Metallschichten geschweißt werden müssen und wo die oben genannten Laser keine optimale Lösung darstellen.
Ein solcher Fall ist das Laserschweißen von Kontakten. Diese Anwendung hat sich in letzter Zeit zu einem Trend entwickelt, auch aufgrund der intensiven Ausweitung der Nutzung von Batteriezellen als Energiequellen. Der Bereich der Elektromobilität ist einer der typischen Bereiche für den Einsatz dieser Anwendung. Die Kontakte sind nicht nur sehr dünn, sondern bestehen häufig aus einer Kombination heterogener, d. h. unterschiedlicher metallischer Werkstoffe wie Ni + Al oder Cu + Al. Beim Schweißen heterogener Werkstoffe mit kontinuierlichen Lasern bilden sich an den Verbindungsstellen der Schichten intermetallische Bereiche, die die Festigkeit der Schweißnaht verringern. Auch aus diesem Grund ist der Einsatz von gepulsten Lasern in diesem Fall vorzuziehen. Natürlich muss, wie bei jeder anderen Schweißung auch, ein guter thermischer Kontakt der geschweißten Lagen, der in der Regel durch einen geeigneten Klemmmechanismus unterstützt wird, gewährleistet sein.
LINTECH nutzt sein Know-how, um heterogene Schweißnähte mit Nanosekunden-Faserlasern mit geringer Durchschnittsleistung zu erzeugen. Diese Laser sind nicht nur in der Lage, selbst sehr unterschiedliche Materialien effizient zu verbinden, sondern bieten auch wirtschaftliche Vorteile, insbesondere im Vergleich zu kontinuierlichen Hochleistungslasern. Schweißnähte werden in der Regel als eine Gruppe von Punkten bestimmter Form und Größe ausgeführt, bei denen Material von der oberen Schicht auf die untere Schicht und umgekehrt übertragen wird. In geringerem Maße kommt es auch zur Bildung von Schmelze, wodurch der negative Effekt des intermetallischen Bereichs unterdrückt wird. Ein weiterer bedeutender Vorteil ist der sehr kleine Wärmeeinflussbereich um die Schweißnaht herum, der das dünne Material nicht verformt und potenziell empfindliche Komponenten in der Nähe nicht beeinträchtigt.
Die Dauer beim Schweißen von Kontakten liegt in der Regel in der Größenordnung von Sekunden, und die erreichbare Schweißnahtfestigkeit kann bis zu 900 N bei Scherung und 200 N bei Zugkräften betragen. Diese Ergebnisse wurden in zahlreichen Zugversuchen wiederholt bestätigt. Die Verwendung einer Schutzgasatmosphäre ist möglich und auch von Vorteil, da sie die Schweißnahtgestaltung und die Prozessstabilität verbessert. Die Verwendung einer Schutzgasatmosphäre ist jedoch nicht unbedingt erforderlich; die Schweißnaht behält ihre Eigenschaften dennoch bei.
Wir haben die Machbarkeit dieser Anwendung bereits mehrfach getestet. Im Jahr 2020 haben wir zum Beispiel das Verschweißen von Nickelbändern mit Batteriezellen untersucht. Die Testergebnisse können Sie in unserem früheren Artikel nachlesen.