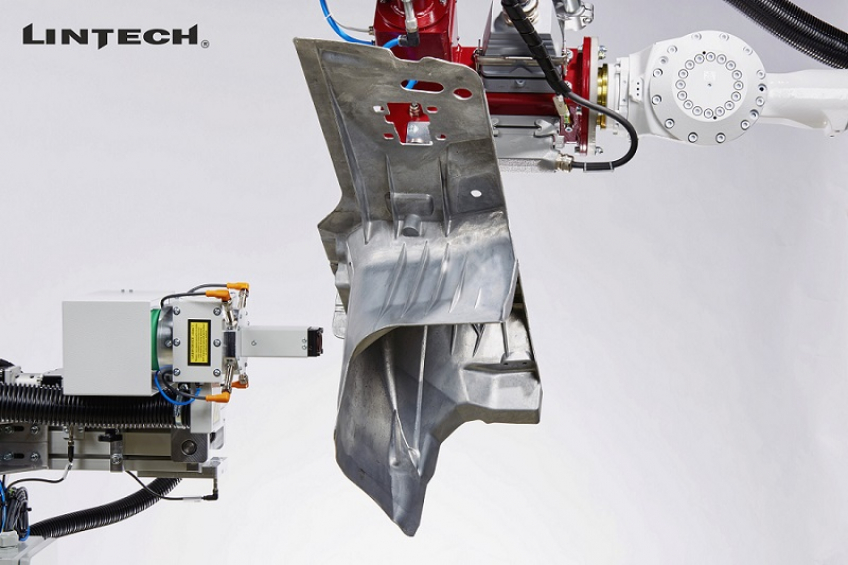
CASE STUDY: LINTECH Laser Safety Head
LINTECH arbeitet seit vielen Jahren eng mit SPI zusammen. Als Integrator von Lasermodulen verwenden wir die SPI-Laser hauptsächlich zum Markieren und Gravieren. Neben der Herstellung von Lasersystemen bieten sie ihren Kunden auch die Dienstleistungen eines Designzentrums an. Als eines der wenigen Unternehmen auf dem tschechischen Markt können sie dem Kunden daher eine umfassende Lösung für das Problem der Laseranwendungen anbieten. Von der Beratung über das Lösungsdesign bis zur endgültigen Lieferung eines kompletten Geräts mit Lasersystem. Im Gegensatz zur Konkurrenz kann LINTECH individuelle Lösungen individuell nach spezifischen Anforderungen und Kundenanforderungen entwerfen.
Das Haupttätigkeitsfeld von LINTECH ist der in der Tschechischen und Slowakischen Republik weit verbreitete Automobilsektor. In den letzten Jahren ist es ihnen dank der Zusammenarbeit mit einem deutschen Partner gelungen, ihr Tätigkeitsfeld zu erweitern, und sie liefern derzeit Lasersysteme in ganz Europa. Einer der Hauptgründe für den Erfolg von LINTECH ist der technische Hintergrund des Anwendungslabors. Dank ihres eigenen Anwendungslabors können sie mit den Innovationen des SPI-Entwicklungszentrums Schritt halten.
Eine neue Herausforderung für Techniker von LINTECH
Vor einigen Jahren haben sie auf einer der Messen, an denen LINTECH regelmäßig teilnimmt, Kontakt zu einem neuen Kunden aufgenommen, der sie gebeten hat, eine Lösung für ihre Produktion vorzuschlagen. Der Antrag betraf den Ersatz der bestehenden mechanischen Kennzeichnung von Aluminiumgussteilen. Die ursprüngliche Mikroschlagtechnologie markierte die Gussteile außerhalb des primären Produktionsstroms an einem separaten Arbeitsplatz. Darüber hinaus befand sich dieser Arbeitsplatz nicht zu Beginn des Produktionsprozesses, sondern es gingen mehrere Produktionsvorgänge voraus. Die Möglichkeit, Produktionsdaten anhand des markierten 2D-Codes zu verfolgen, war aus Effizienzgründen nicht ideal und unzureichend. Die Aufgabe von LINTECH bestand darin, ein mit einem Roboterarm zusammenarbeitendes Lasergerät zu entwickeln, das die Verbesserung des Markierungsprozesses gewährleistet und gleichzeitig die Verwechslungsgefahr von Aluminiumgussteilen durch manuelle Handhabung des Gussstücks beseitigt.
Die von LINTECH vorgeschlagene Lösung war die Schaffung eines mit einem Roboterarm kompatiblen Lasergeräts, das den Datamatrix-Code unmittelbar nach dem Entfernen aus dem Gießgerät, dh gleich zu Beginn des Produktionsprozesses, in ein Aluminiumgussstück eingraviert. Durch die Kennzeichnung zu diesem Zeitpunkt in der Produktion können alle erforderlichen Attribute (genaue Gießzeit, Temperatur,…) in den gekennzeichneten 2D-Code eingegeben werden, und gleichzeitig wird der Austausch gekennzeichneter Teile verhindert.
Aus technischer Sicht brachte dies mehrere Herausforderungen mit sich. Das Produkt wurde mittels eines Roboterarms aus der Gießmaschine entfernt. Anschließend wurde es in einem Wasserbad gekühlt. Auch nach dem Abkühlen lag die Temperatur des Produkts über 100 ° C. Restliches Wasser auf der behandelten Oberfläche musste entfernt werden, um die Stabilität des Prozesses zu gewährleisten. Gleichzeitig war ein Szenario möglich, in dem das Produkt von der Gießanlage direkt zur Markierung gelangt und die Temperatur des verarbeiteten Teils 200 ° C überschreitet. Neben der Temperatur war es natürlich notwendig, den Sicherheitsaspekt zu lösen, da das vorgeschlagene Gerät die Sicherheitsklasse Nr. 1 erfüllen musste.
Warum einen Laser anstelle eines Nadelprägers?
In den meisten Fällen wird die Markierung solcher Gussteile unter Verwendung der Mikropunkttechnologie durchgeführt. Der Mikropunkt erzeugt mit einer Hartmetallspitze kleine Grübchen in den Gussteilen, wobei jedes Loch ein einzelnes Modul im 2D-Code darstellt. Das Material wird mit der Spitze relativ tief unter die Oberfläche des Teils gedrückt, was einen hohen Widerstand des markierten Codes gewährleistet. Die Geometrie des Grübchens hängt von der Form der Spitze ab, insbesondere von ihrem Schleifwinkel.
Damit der 2D-Barcode leicht lesbar ist, muss ein ausreichender Kontrast zwischen dem betroffenen und dem nicht betroffenen Material hergestellt werden. Es ist nicht möglich, durch Ändern der Oberflächenfarbe standardmäßig einen Kontrast zu erzeugen, da die Oberfläche des Teils während der folgenden Vorgänge erheblich behandelt wird und die Farbe von der Oberfläche verschwindet. Der Mikropunkt färbt die Oberfläche des Materials nicht, sondern erzeugt durch geeignete Beleuchtung einen Schatten innerhalb der geprägten Grübchen, um den Dunkelheitseffekt auf der Oberfläche zu simulieren.
Ein ähnliches Prinzip zum Erstellen von 2D-Code wurde mit dem gepulsten Laser verwendet. Ein ausreichend leistungsfähiger gepulster Laser kann Module mit einer ähnlichen Effizienz wie ein Mikropunkt in Aluminiummaterial gravieren. Im Gegensatz zu einem Mikropunkt haben lasergravierte Module jedoch eine Reihe von Vorteilen.
Der Laser ist sehr genau und weist eine hohe Wiederholgenauigkeit auf. Dadurch wird eine hohe Ähnlichkeit der einzelnen Module erreicht, was das Lesen erleichtert. Die Wände der lasergravierten Module weisen eine viel größere Rechtwinkligkeit auf, so dass sich in ihnen besser Schatten bilden. Die Tiefe der Gravur hängt von der Anzahl der Wiederholungen des Gravurprozesses ab und ist daher gut skalierbar, um das optimale Verhältnis zwischen Zeit und Tiefe zu erzielen. Der Laser kann sehr einfach und gut auch sehr komplizierte Begleitmuster oder Logos gravieren. Im Gegensatz zu einem Mikropunkt, bei dem die Prägespitze beim Kontakt mit dem Material abbrechen und anschließend Schrottflecken bilden kann, ist der Laserprozess sehr robust und stabil. Da der Laser während des Vorgangs keine Kraft auf das Teil ausübt, muss das Teil während des Markierungsvorgangs im Gegensatz zu einem Mikropunkt nicht mit einer größeren Kraft gehalten werden.
Dank der oben beschriebenen Fakten erreichte die Qualität der gravierten Codes mit einem gepulsten Laser bei Verifizierungsmessungen standardmäßig bessere Werte als bei Codes, die von einem Mikropunkt gebildet wurden, insbesondere nach nachfolgenden Oberflächenbehandlungen. Es stellte sich heraus, dass zur Gewährleistung der Lesbarkeit auch nach der Oberflächenbehandlung eine Gravurtiefe zwischen 0,2 und 0,3 mm erreicht werden muss, die mit einem Lasersystem mit SPI 100P-EP-Z-Modul in ca. 10 s erreicht werden kann, wobei die Verarbeitungszeit natürlich stark abhängig ist auch auf die Größe und Artikulation des Codes. Aufgrund seiner Strahlqualität von weniger als 1,6 und der hohen Durchschnittsleistung erwies sich der 100P-EP-Z-Laser als sehr geeignet für den gesamten Betrieb.
Lösung
Um einen angespannten Produktionszyklus verfolgen zu können, muss zum Gravieren ein gepulster Laser mit einem Mindestwert von durchschnittlich 70 W verwendet werden. Mit einer höheren Leistung können Sie die Verarbeitungszeit weiter verkürzen. Basierend auf Langzeittests wurde der am besten geeignete Laser für diese Anwendung 100P-EP-Z ausgewählt, wodurch innerhalb der gegebenen Anwendung eine höhere Effizienz erzielt wurde. Gegenüber der 70W-Variante lag die Effizienzsteigerung bei rund 30%. Als Fokussieroptik wurde eine F-Theta 210-Linse verwendet.
Dieses Objektiv hat aufgrund des Designs unserer Abdeckung nicht nur eine geeignete Fokussierentfernung, sondern auch ein gutes Verhältnis zwischen der Größe der Laserspur und der Flächenenergiedichte. Auf diese Weise können Sie große Materialmengen pro Zeiteinheit effizient und kontrolliert gravieren.
Die Verwendung eines Lasers führt natürlich zu bestimmten Fallstricken. Diese können jedoch mit geeigneten Verfahren und Entwurfsmaßnahmen erfolgreich gelöst werden. Die größte Herausforderung besteht darin, die erforderlichen Sicherheitsstandards für die Arbeit mit Lasern einzuhalten, bei denen der Arbeitsstrahl effektiv von der Umgebung abgeschirmt werden muss, um die Sicherheitsklasse I zu erfüllen. Dies wird durch eine Reihe von Sensoren unterstützt, die sich auf einer speziellen Laserkopfabdeckung befinden und den Laser ausschalten, wenn ein Leck erkannt wird. Laserraum. Da die Lasergravur ein großes Volumen an Verunreinigungen erzeugt, müssen diese während des Prozesses intensiv abgesaugt werden, um den Laserstrahl nicht in Richtung der gravierten Oberfläche zu blockieren.
Fazit
Die endgültige Form des von LINTECH entworfenen kompakten Laserkopfs hat alle Belastungs- und Sicherheitstests bestanden. Daher gelang es ihm, die Ausschreibung auf Kosten des in- und ausländischen Wettbewerbs durchzuführen. Das Design des LINTECH-Abdeckkopfs und des SPI-Pulsfaserlasers führte zu einer sehr positiven Kundenresonanz. Die Integration dieser kompakten Abdeckköpfe wurde auf die Muttergesellschaft des LINTECH-Kunden und damit auf nahezu alle Niederlassungen weltweit ausgeweitet.
Link zu einer Fallstudie auf der SPI.